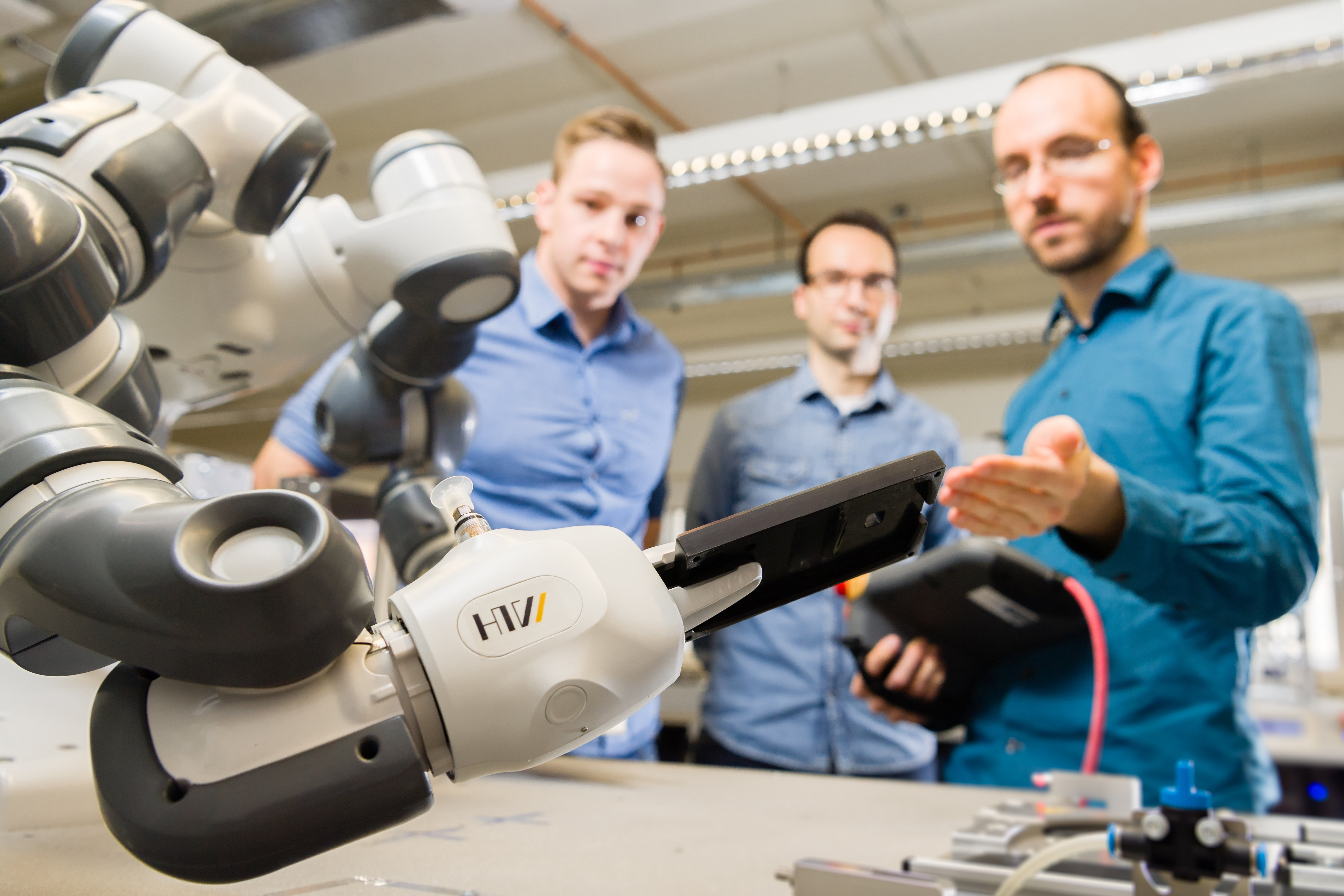
Forschungs- und Entwicklungsprojekte
Aktuelle Forschungsprojekte
ASYN4CVA
Im Projekt ASYN4CVA soll ein durchgängiges Verfahren zur automatisierten Erzeugung synthetischer Bilddatensätze und der Aufbau eines robusten Objekterkennungsmodells für kundenspezifische Produkte entwickelt werden.
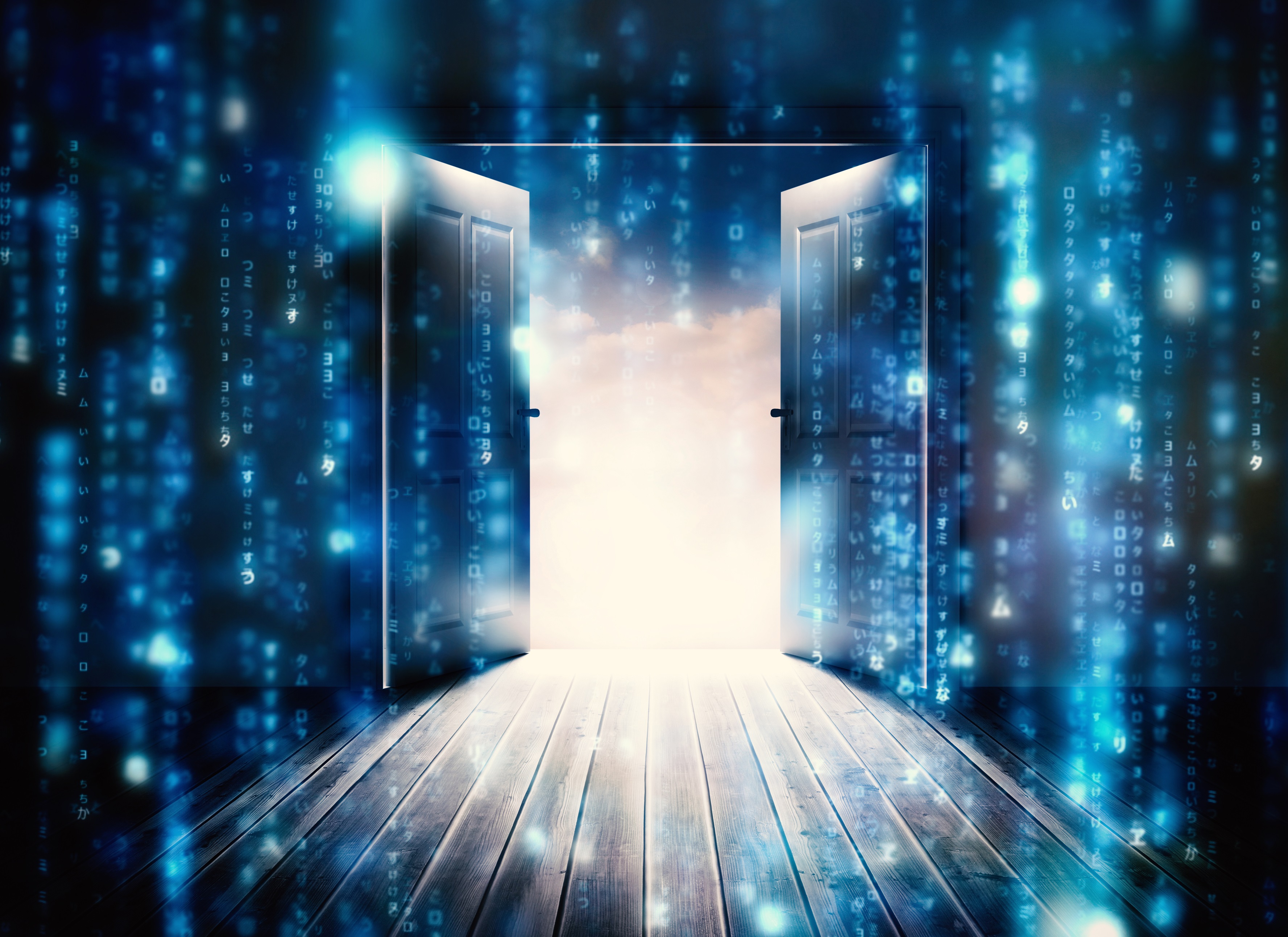
ICV - Industrial Computer Vision
Im Rahmen des Projektes ICV sollen die Prüfung der vielfältigen visuellen Inspektionen in der Produktion mithilfe von Computer Vision evaluiert werden.
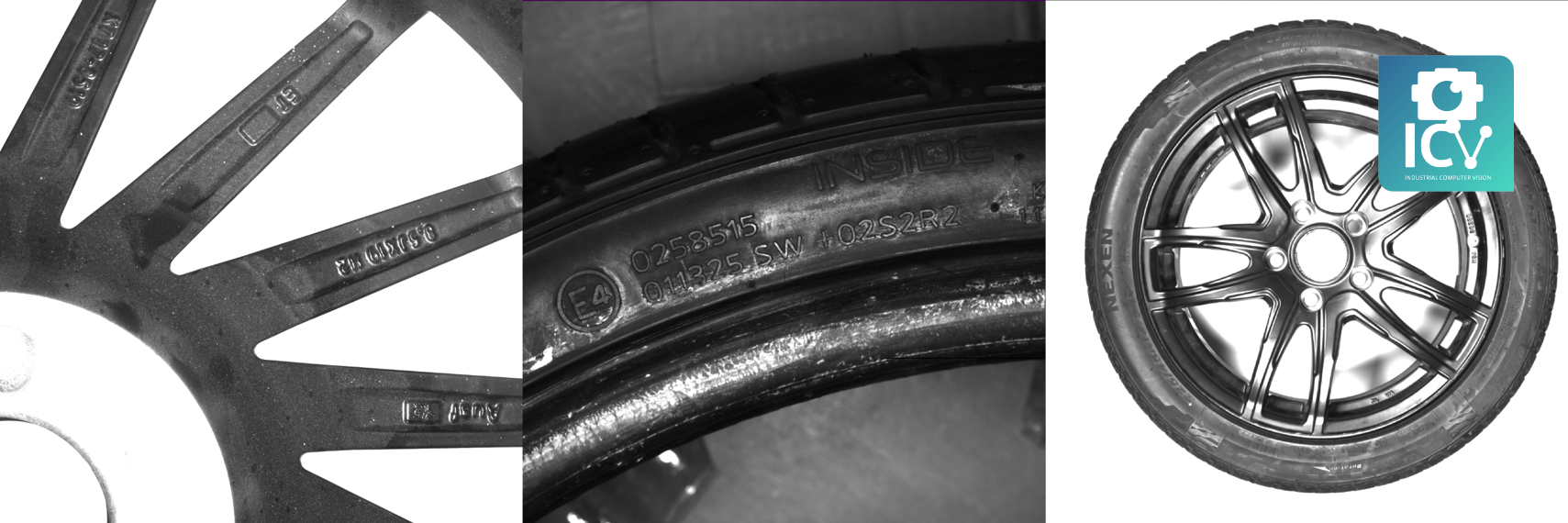
KISS-MINT
Kreativ, Interessant, Spielerisch Sensibilisieren für MINT mit Unterstützung des TÜV Süd und in Zusammenarbeit mit Dresdner Schulen entwickelt die HTW Dresden im Projekt KISS-MINT neue Experimente für den schulischen Alltag mit dem Calliope Mini.
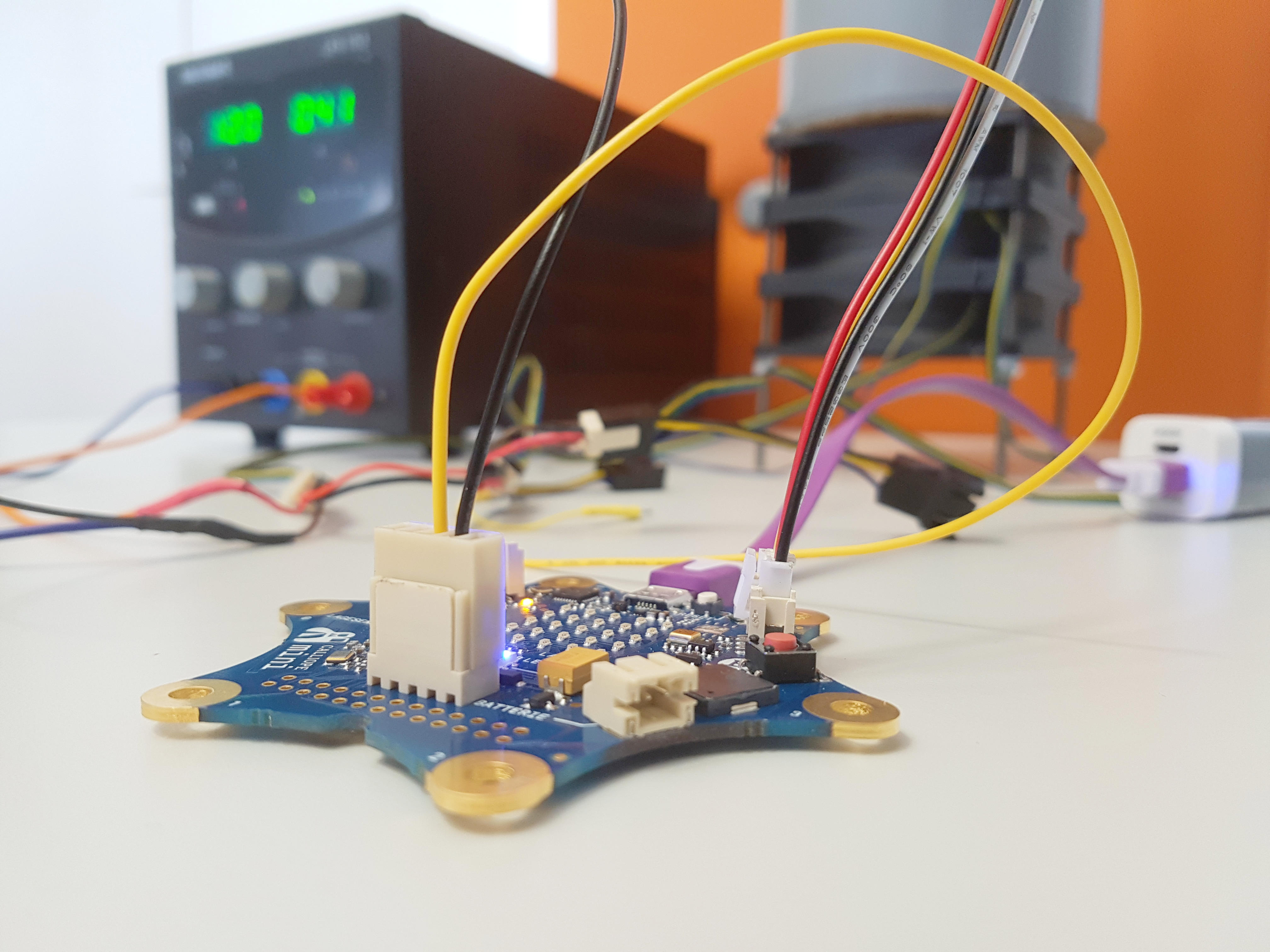
Lab X - das Start Up Lab
Im Rahmen des Projektes Lab X wird eine Interdisziplinäre Ideenwerkstatt für Prototyping und zum Austauschen und Entwickeln von Ideen zur Förderung von StartUps geschaffen.
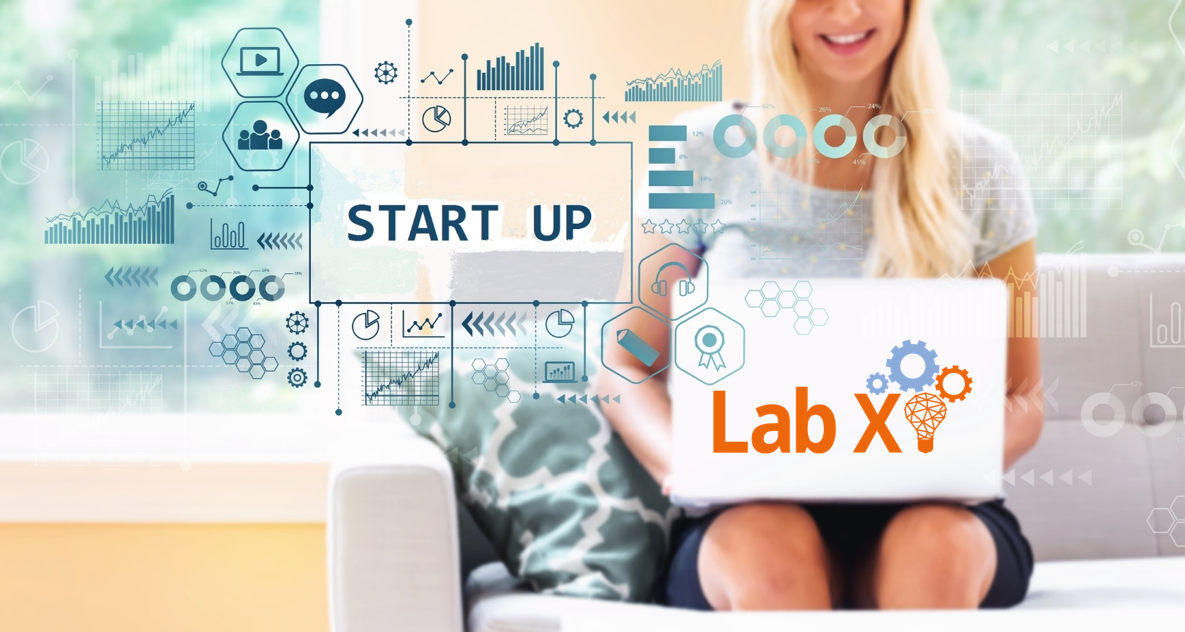
oShop
Das Projekt oSHOP stellt das Konzept Open Source Hardware (OSH), frei zugängliche Baupläne für physische Komponenten, Geräte und Maschine in den Mittelpunkt des Forschungstransfers.
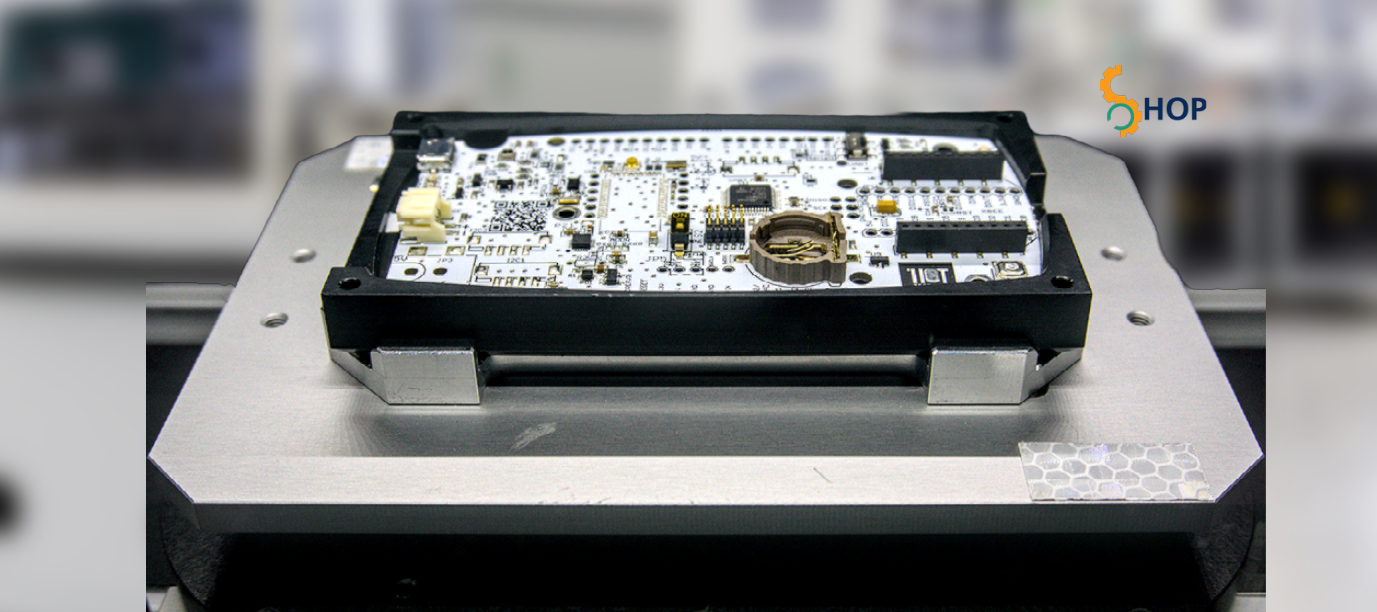
P3S2
P3S2 steht für persönliches, portabeles und präventives Schutzsystem. Es soll die Erweiterung der klassischen persönlichen Schutzausrüstung durch sensorische, aktorische und kommunikative Fähigkeiten untersucht werden.
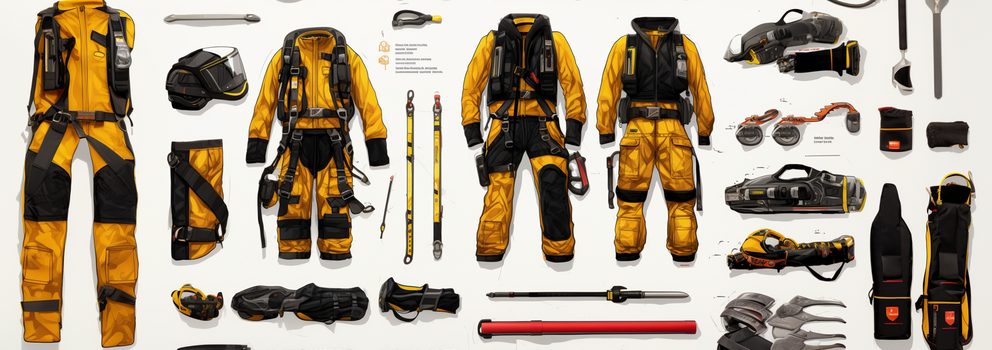
Industrie 4.0 Modellfabrik
Im Projekt ist eine zentrale Labor- und Forschungsinfrastruktur entstanden, die zur interdisziplinären Erforschung und Entwicklung von Industrie4.0-Konzepten und Lösungen in der Lehre und Praxis eingesetzt werden kann.
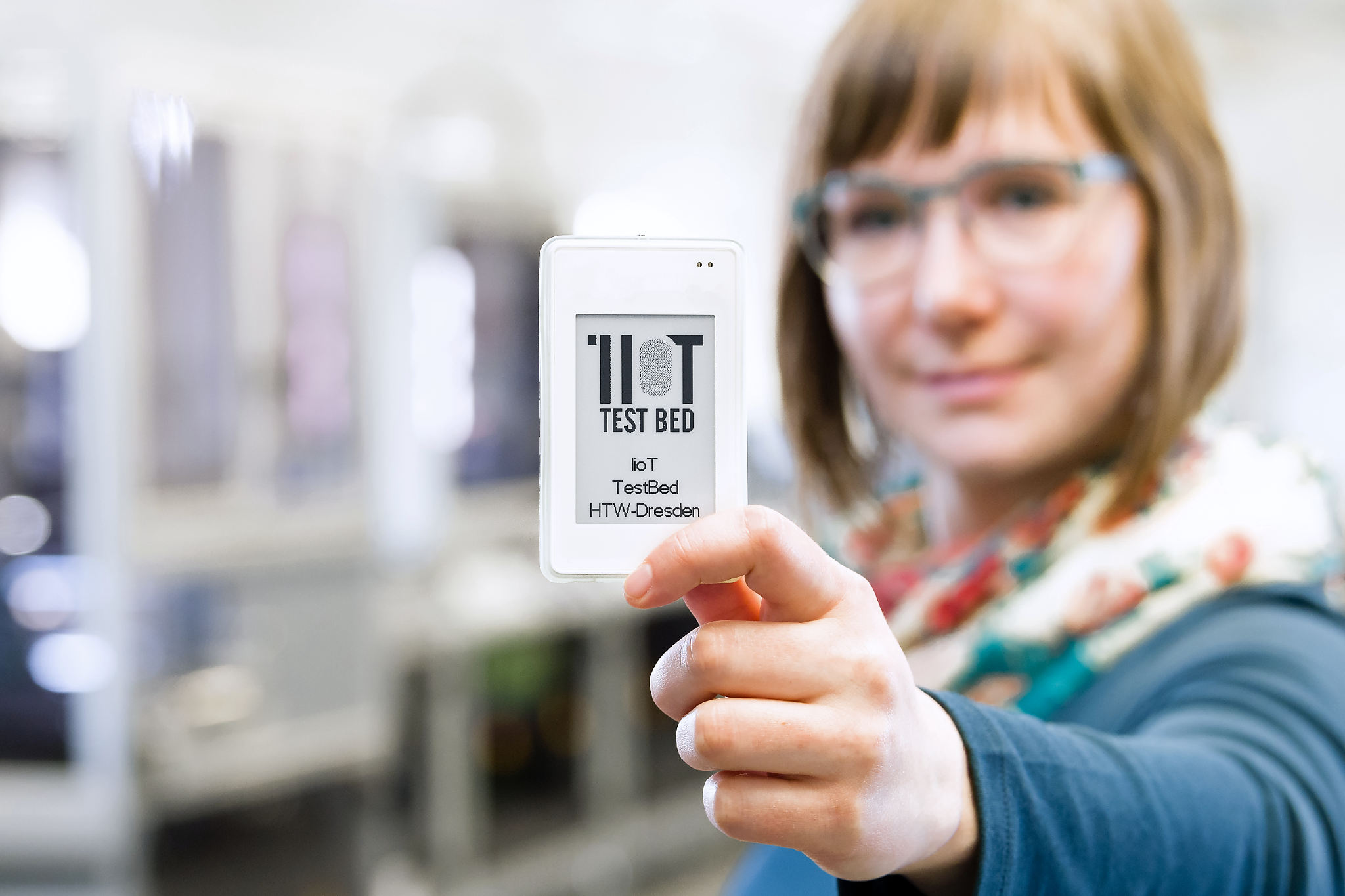
Clever
CLEVER entwickelt eine Reihe von Innovationen im Bereich der Hardware-Beschleuniger, des Design-Stacks und der Middleware, die die Fähigkeit von Edge-Computing-Plattformen revolutionieren, föderativ zu arbeiten und spärliche Ressourcen zu nutzen.
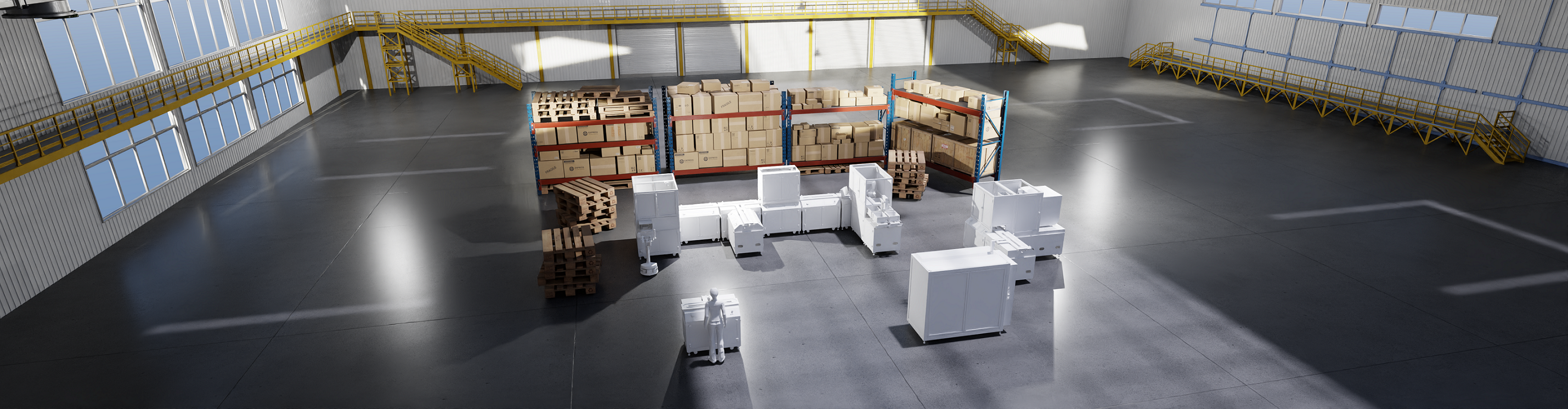
Future Mobility
Das durch Infineon Technologies Dresden GmbH & Co. KG geführte Verbundprojekt Future Mobility zielt darauf ab, entlang der gesamten Wertschöpfungskette, innovative Lösungen für zukünftige Automobilelektronik zu erarbeiten.
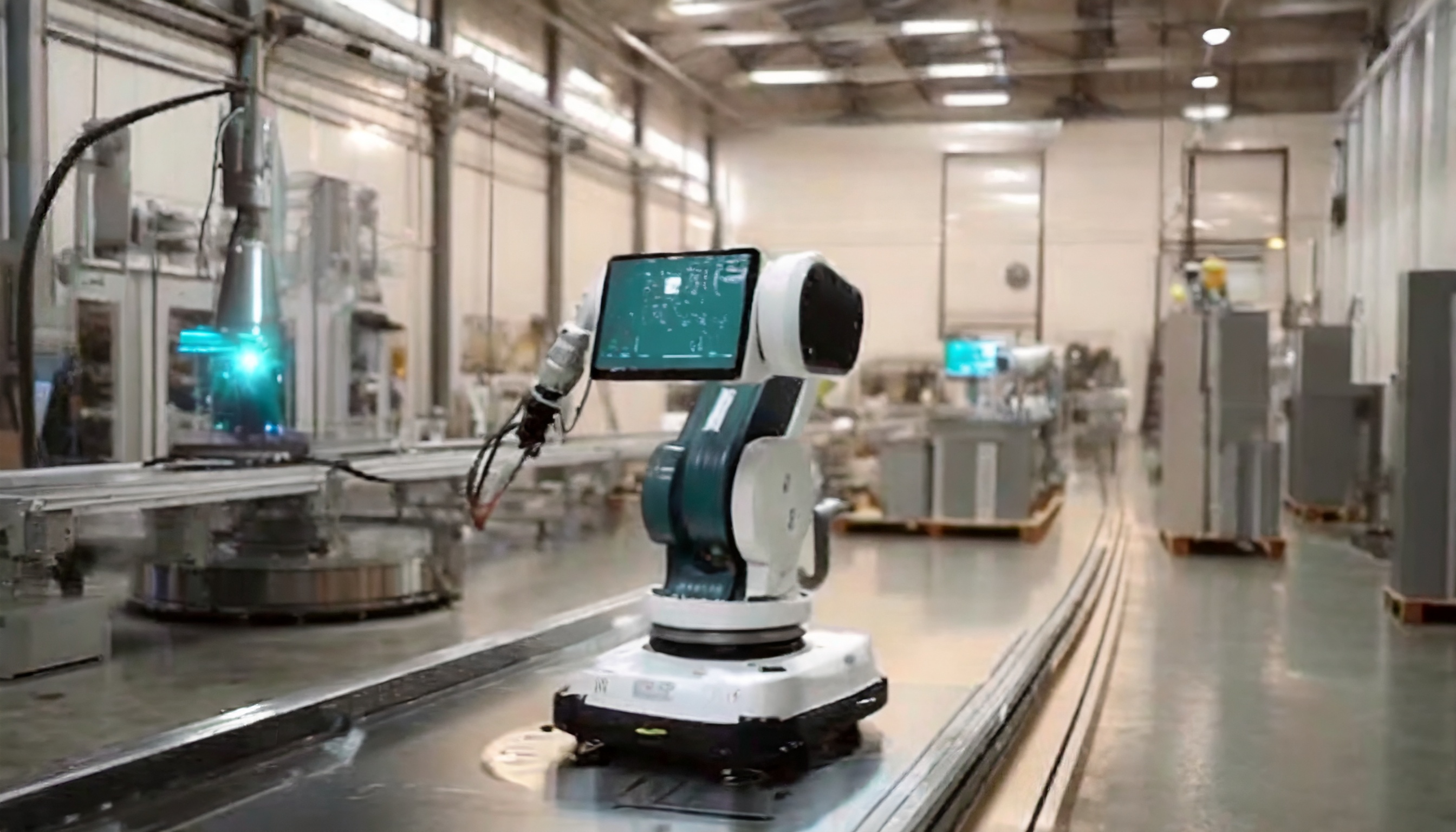
KiWi
Mit dem Projekt "KiWi – KI-Werkstatt: für den Transfer in die Wirtschaft" soll die Rolle der HTW am Standort Dresden gestärkt werden, um so langfristig Fähig- und Fertigkeiten im Bereich KI zu schaffen, zu verstetigen und zu bündeln.
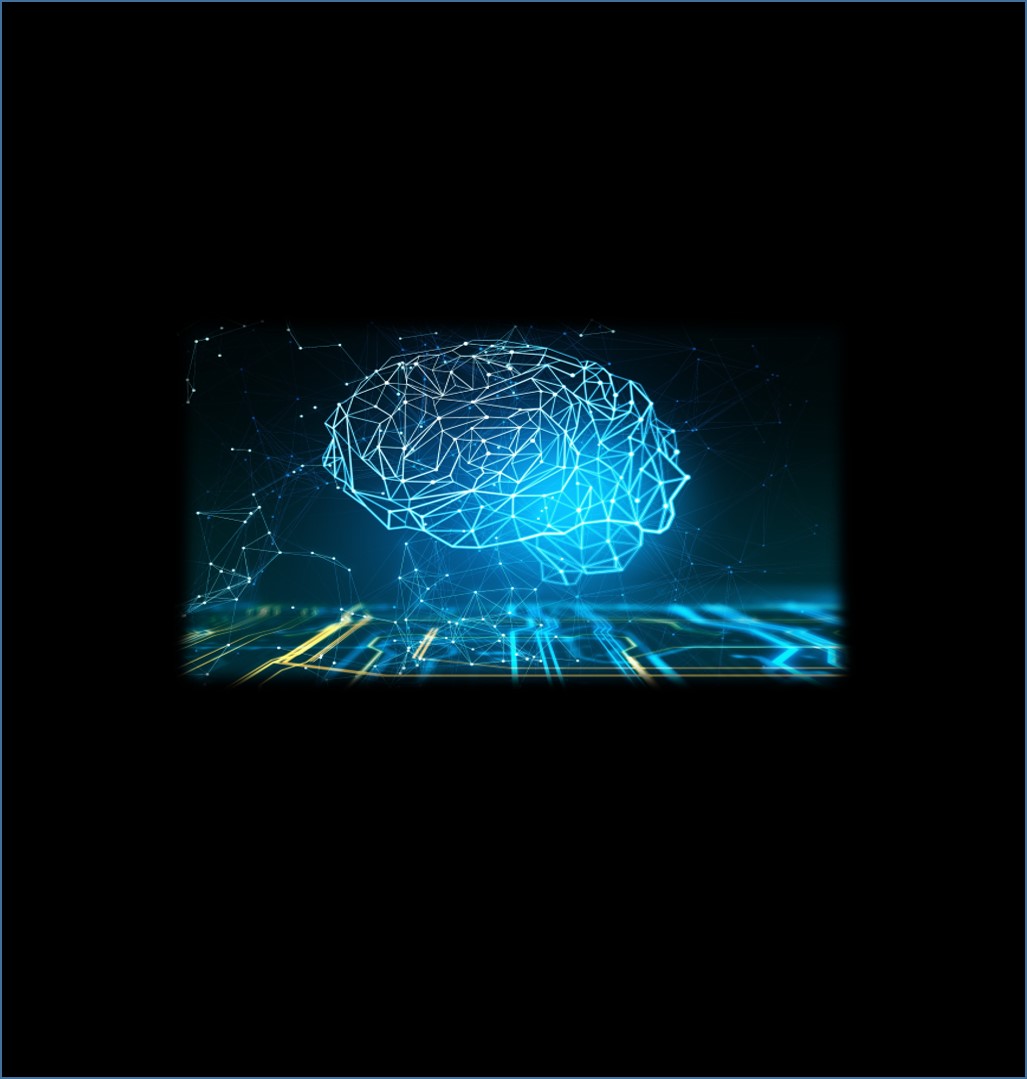
LOTSE
Das Projekt LOTSE erforscht und entwickelt gemeinsam mit Globalfoundries neue Methoden, um in der Halbeleiterfertigung auch bei kurzfristigen und häufigen Bestelländerungen jederzeit termingerecht liefern zu können.
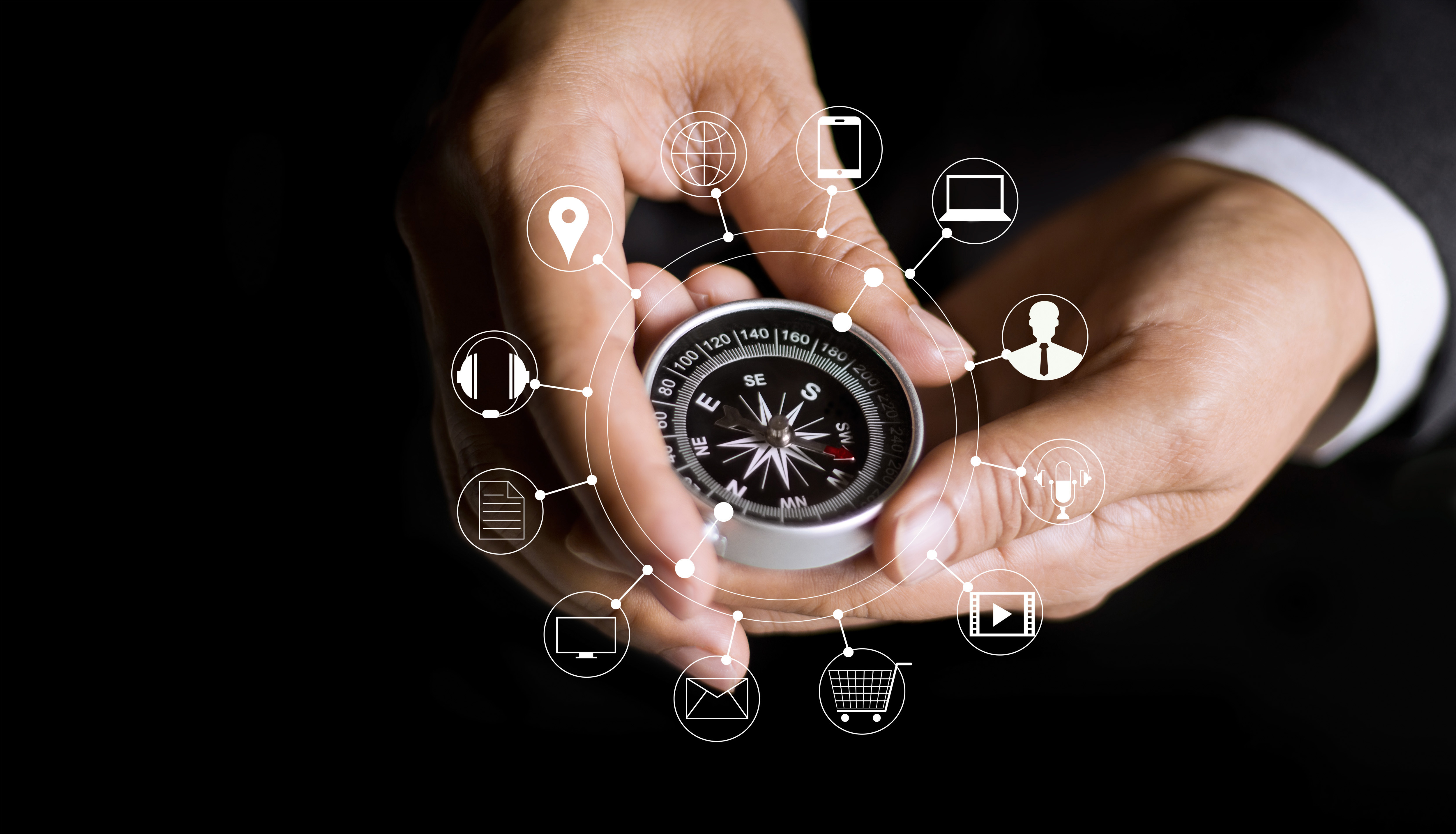
OSHIE
Das Projekt OSHIE zielt darauf ab, die Nutzung von freier und offener Hardware für wissenschaftliche Aufgaben für das Wissenschaftssystem zu untersuchen.
ProMenTaT
Im Fokus der Nachwuchsforschungsgruppe „Produktionssysteme mit Menschen und Technik als Team“ (ProMenTaT) steht die Erforschung der Rollen und Aufgaben, die Menschen als Individuen in künftigen Produktionssystemen einnehmen.
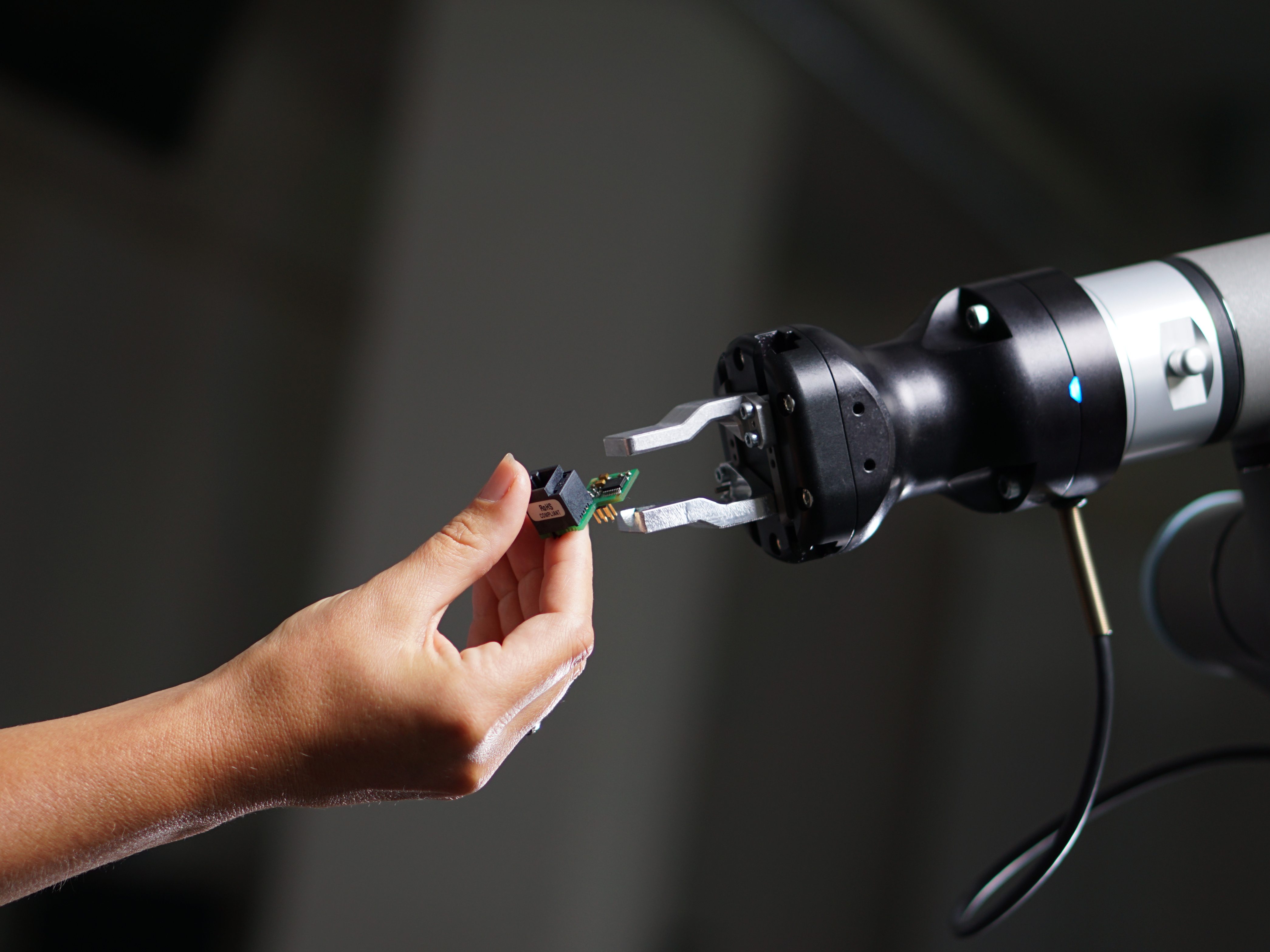
Saxony5 Transferfeld "Produktion"
Das Transferfeld "Produktion" im Transferverbund Saxony5 befasst sich mit der Themenstellung "Resiliente Fertigung".
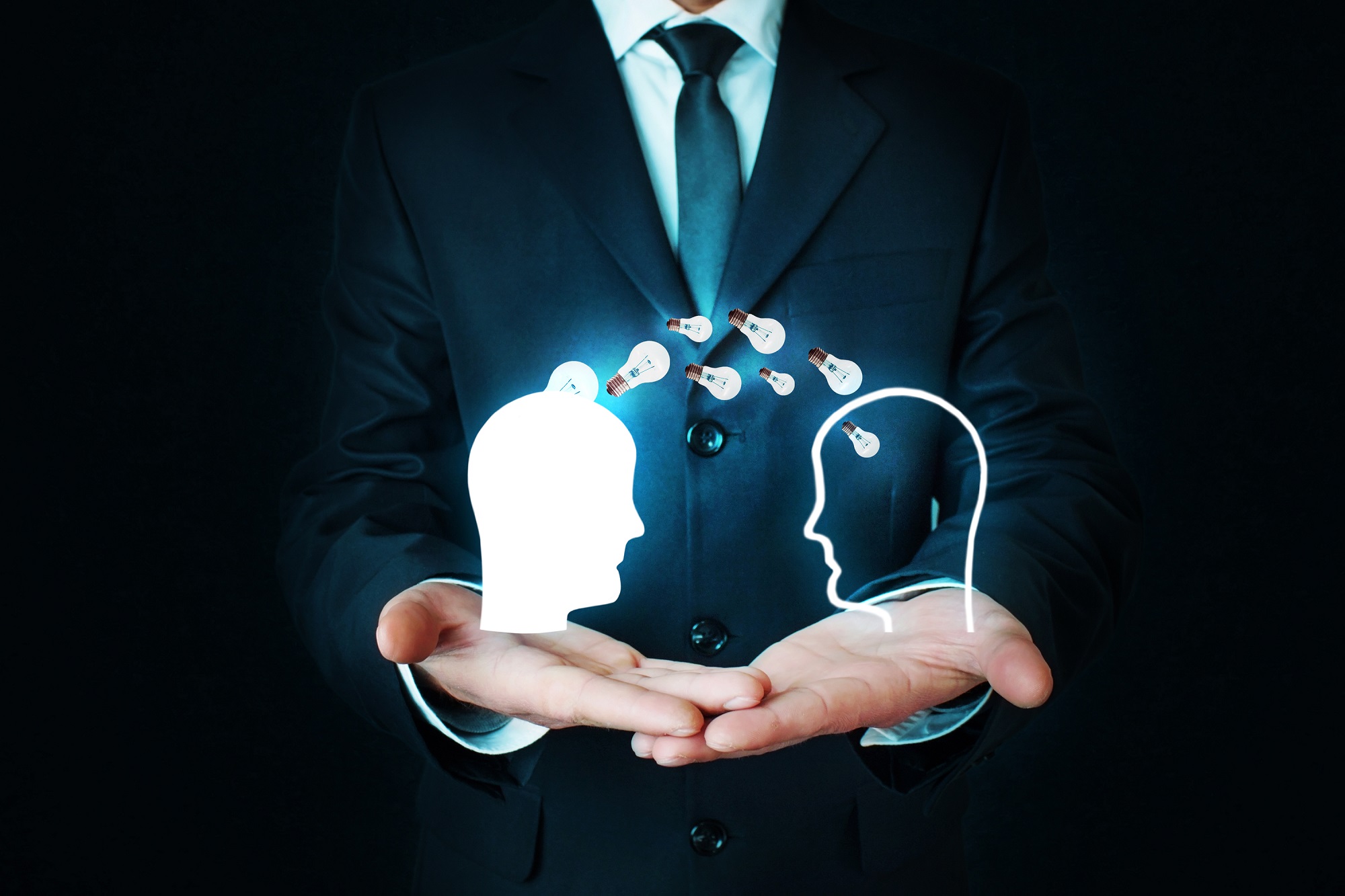
Semiconductor-X
Das Projekt »Semiconductor-X« hat zum Ziel auf Basis der Gaia-X/Catena-X-Architektur digitale Zwillinge für die Halbleiterindustrie zu entwickeln, welche das planungskritische Segment der Liefer- und Wertschöpfungskette digital abbilden.
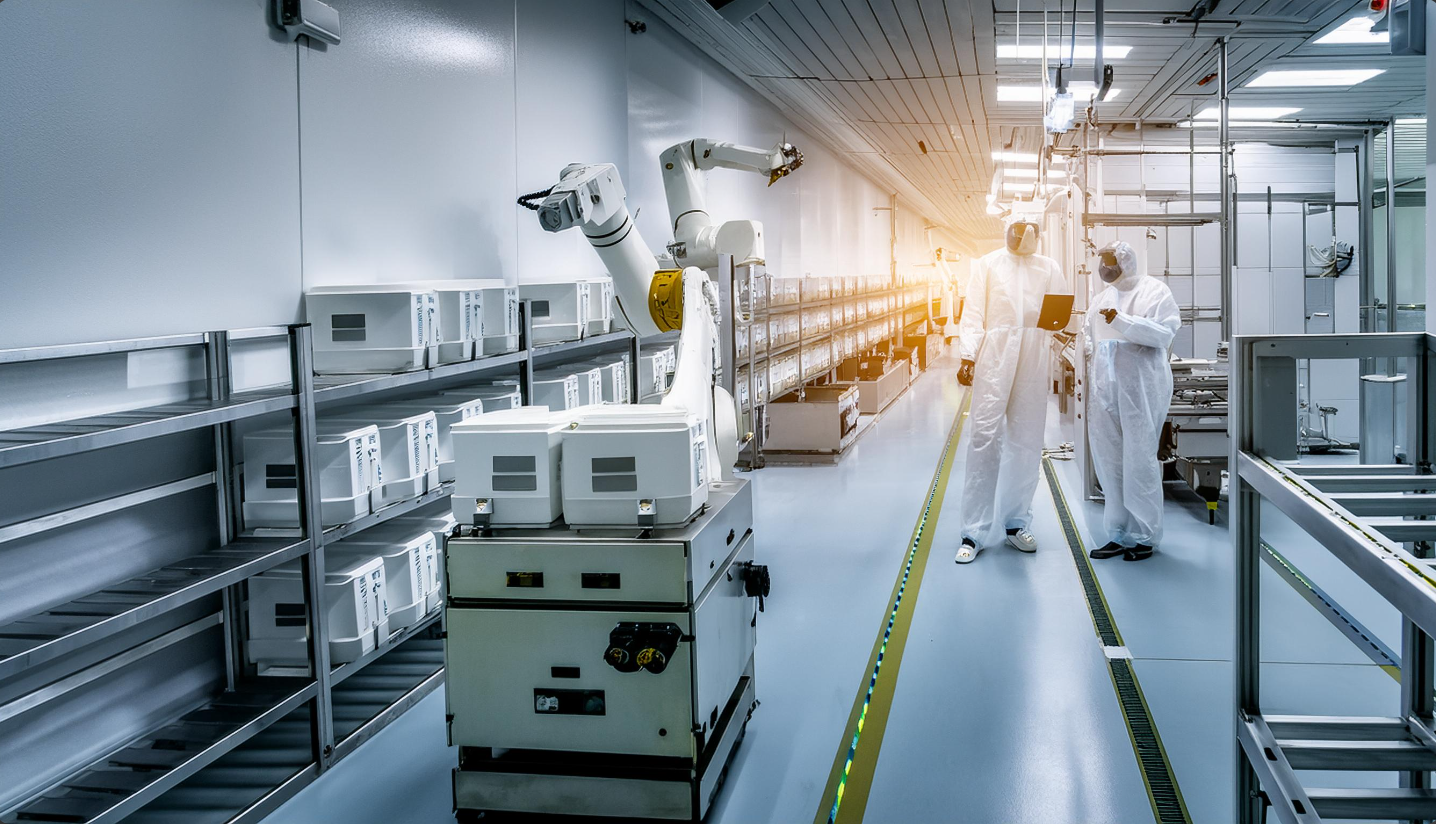
Eigenes Projekt starten?
Gern können Sie mit uns Kontakt aufnehmen bei Interesse und bei spannenden Ideen für gemeinsame Projekte! Wir helfen gern bei einer genaueren Ideenfindung und Validierung Ihrer Produktinnovation.
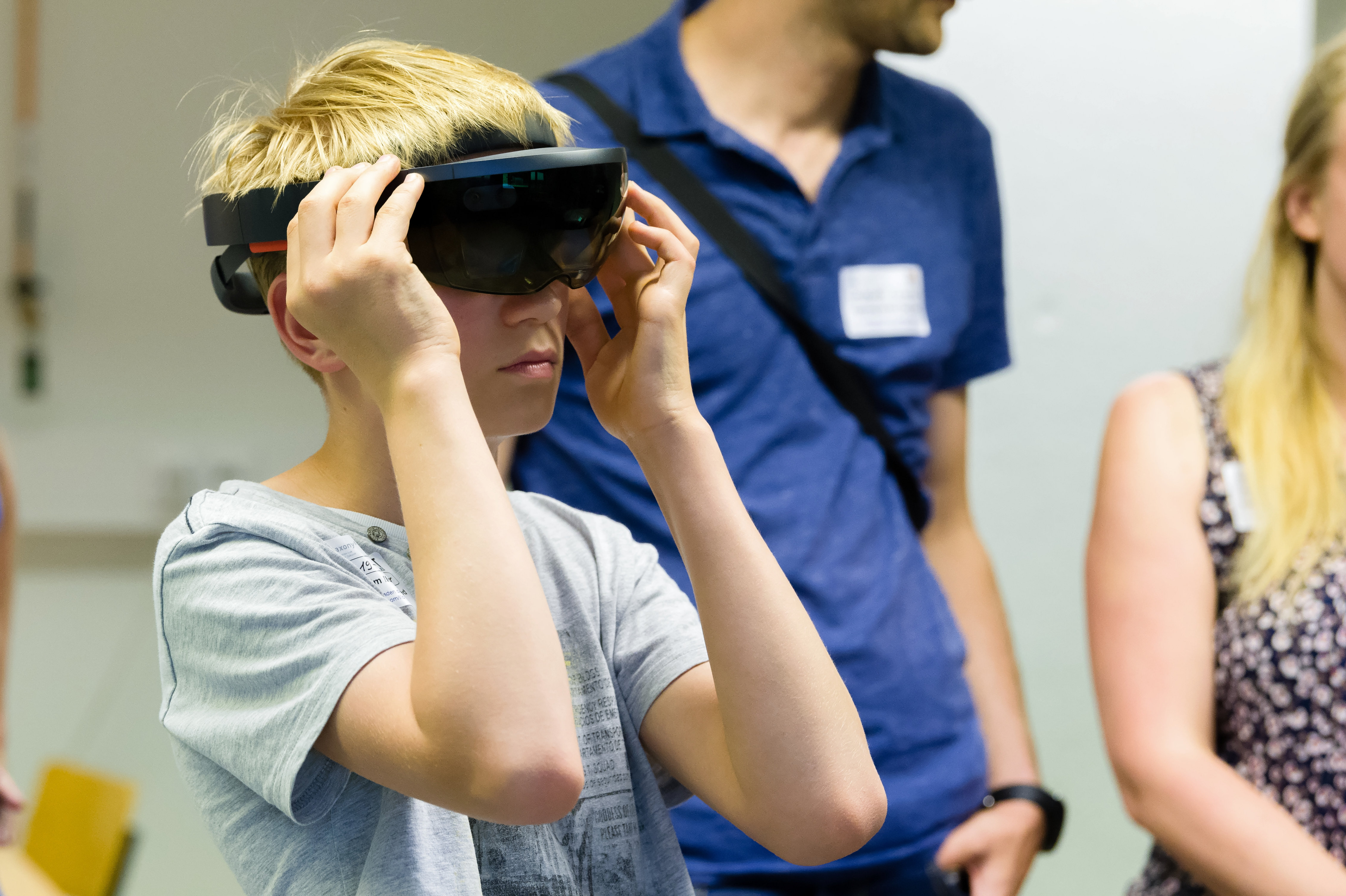
Abgeschlossene Forschungsprojekte
In der Produktionstechnik werden sekündlich enorme Datenmengen erzeugt und in den produzierenden Maschinen intern verarbeitet. Diese Daten beinhalten wertvolle Hinweise auf den aktuellen Zustand von Maschine, Werkzeug und Produkt und könnten durch gezielte Auswertung das Wertschöpfungspotenzial der Maschine und dazugehöriger Dienstleistungen steigern. In der Praxis werden diese Daten jedoch bisher weder umfänglich ausgewertet noch für nachgelagerte Anwendungen, ob unternehmensintern oder -extern, digital bereitgestellt. Gründe hierfür liegen zum einen in den hohen Anforderungen der Datenakquise und -bereitstellung an die maschinennahe Hard- und Software. Zum anderen sind die Investitionen in die digitale Infrastruktur durch noch unklare Amortisation für die Kunden sowie mit Risiken für geistiges Eigentum und Knowhow assoziiert. Gleichzeitig besitzen die Hersteller der Maschinen und ihrer Komponenten zwar das notwendige Knowhow für die Konzeption datengetriebener Anwendungen, jedoch fehlt ihnen der Zugang zu den Daten ihrer Produkte im laufenden Betrieb bei den Kunden. Mit GAIA-X ist ein Rahmen entstanden, in dem datengetriebene Anwendungen unter Beachtung des Datenschutzes und der Datenhoheit realisiert werden können. Im Projekt Fed-X-Pro wird die domänen- und unternehmensübergreifende Dateninfrastruktur von GAIA-X genutzt, um universell einsetzbare Anwendungen zur Wertschöpfungssteigerung in der Produktionstechnik zu realisieren.
Praxispartner
- Fraunhofer-Institut für Werkzeugmaschinen und Umformtechnik IWU (Projektkoordination)
- VPD Vakuum- und Präzisionsteilefertigung Dresden GmbH
- GROB-WERKE GmbH & Co. KG
- Gühring KG
- UKM Technologies GmbH
- Katulu GmbH
- Simplifier AG
Promotionsvorhaben: Entwicklung einer generischen Methode zum Untersuchen zeitlicher Variabilität in Produktionssystemen zur Verbesserung der Produktionsplanung und -steuerung
Die von intelligenten Produktionssystemen generierten Daten bergen ein weitaus größeres Verbesserungspotenzial als derzeit genutzt wird. Als Beispiel fungiert die Unbeherrschbarkeit von Produktionssystemen. Produktionssysteme sind aufgrund der Vielzahl an auf sie einwirkendenden Einflussgrößen komplexe Gebilde stochastischer Natur. Sie sind von zufälligen, unvorhersehbaren Ereignissen sowie bewusst provozierten Ereignissen betroffen. Jedes solcher Ereignisse birgt das Potenzial eines störenden Einflusses.
Das Ziel des Promotionsvorhabens war die Entwicklung einer Methode zum Einbeziehen der Summe an auf ein Produktionssystem einwirkenden Ereignisse in die Planungsprozesse. D.h., dass über die zu entwickelnde Methode das Untersuchen von Variabilität in Produktionssystemen ermöglicht wird. Für eine ideale Kapazitätsvorhersage und -planung des Produktionssystems muss jedes Ereignis berücksichtigt und in dem Grad seiner Einwirkung miteinkalkuliert werden. Gegenwärtige Ansätze arbeiten mit Planungsmethoden, welche die durch die Komplexität hervorgerufene Dynamik des Produktionssystems unzureichend berücksichtigen. Die Datengrundlage basiert vorrangig auf starren Werten. Während sich die Verfügbarkeitsdaten von Arbeitsstationen anhand ihrer Ausfallzeiten über die Produktionszeiträume dynamisch ändern, werden Prozessdaten in der Regel gemessen und/oder berechnet, sowie anschließend als Festwerte im Arbeitsplan hinterlegt. Als fehlende Berechnungsgröße wird die inhärente Variabilität von Produktionssystemen identifiziert, welche es zu erfassen, messen und quantifizieren gilt. Ist der Grad des Einflusses an variabilitätsverursachenden Ereignissen bekannt und lässt sich die daraus resultierende Variabilität quantifizieren, kann diese für zukünftige Planungen mitberücksichtigt werden. Das Leistungsvermögen des Systems lässt sich dann realitätsnah abbilden, sodass Plan- bzw. Zielwerte verlässlich gesetzt werden können. Das resultiert in eine hohe Planungsgenauigkeit, was die Einhaltung des Produktionsprogrammplans gewährleistet und die Erfüllung von Lieferterminen sicherstellt. Die Erfüllung von Lieferterminen wirkt sich positiv auf das Servicelevel aus. Ein positives Servicelevel spiegelt sich in einer hohen Kundenzufriedenheit wider, welche einen wettbewerbsentscheidenden Faktor darstellt.
Des Weiteren lassen sich erkannte Ursachen für inhärente Variabilität gezielt durch Verbesserungsmaßnahmen minimieren, was die Systemleistung erhöht und eine effiziente Ressourcennutzung begünstigt.
Sichere Digitale Identitäten - im Kontext von Industrie 4.0 Anwendungen
Im Rahmen des Projektes ID-Ideal sollte der Umgang mit digitalen Identitäten in Wirtschaft und Verwaltung sicherer und einfacher gestaltet werden. Der moderne Mensch besitzt im Durchschnitt ca. 70 digitale Identitäten. Das Management dieser Identitäten, als auch die Hoheit und Sicherheit über die mit diesen Identitäten verknüpften eigenen Daten zu behalten, ist den meisten Menschen nach Stand der Technik unmöglich. ID-Ideal möchte diese vielen IDs deswegen durch eine einzige sichere digitale ID ersetzen und eine Basis für bestehende und künftige digitale Identitätsdienste und breitenwirksame Alltagsanwendungen schaffen. Die Basis ist das sogenannte ID-Ideal Trust Framework, es regelt die technische, semantische und rechtliche Interoperabilität von Diensten und Anwendungen.
Die Forschungsziele für den Schwerpunkt Industrie 4.0 WAREN:
1. Generisches Integrationskonzept zur universellen Anbindung von digitalen ID-Lösungen an cyber-physische Assets
2. Sichere Identifizierung über standardisierte Protokolle zwischen industriellen Maschinen
3. Abbildung von systemspezifischen Identifikationsmerkmalen in einheitlichen Informationsmodellen
4. Automatisierte ID-Management per Verifiable Credentials von cyberphysischen Assets
Motivation
Mit Hilfe von Industrie 4.0-Szenarien ist eine effektive und effiziente Fertigung individueller Kundenwünsche möglich. Dies ist wesentlicher Bestandteil für zukunftsorientierte Unternehmen und Forschungsgegenstand der 5 sächsischen Hochschulen für angewandte Wissenschaften und dem Fraunhofer-IPMS. Das Co-Creation Lab (CCL) bündelt die Potenziale in dem Transferverbund Saxony5. Der Fokus dabei liegt auf der Schaffung einer interdisziplinären Forschungsumgebung. Das Kernelement bildet das Industrial Internet of Things (IIoT) Test Bed der HTW Dresden, welches durch weitere Laboreinrichtungen zu einer virtuellen, über ganz Sachsen verteilten, Fabrik wird. Diese sind zum Beispiel Elemente der kollaborativen Robotik der Hochschule für Technik, Wirtschaft und Kultur Leipzig (HTWK) und Hochschule Mittweida (HSMW), eine Smarte Factory der Westsächsischen Hochschule Zwickau (WHZ) und Labortechnik zur Forschung im Bereich betrieblicher Gesundheitsschutz an der Hochschule Zittau/Görlitz (HSZG). Vernetzt und verbunden wird diese Forschungsinfrastruktur über das CCL innerhalb der Saxony5-Standorte. Neben dem Kompetenzaustausch soll eine Erforschung in den Feldern Technologietransfer und Projektanbahnung und -bearbeitung durch die Zusammenarbeit mit Industriepartnern erfolgen. Mit der Bündelung der Kompetenzen entsteht ein Transferverbund, welcher die wesentlichen Kernelemente für den digitalen Wandel in der Fertigung bündelt und eine zentrale Anlaufstelle für Unternehmen zum Thema Fabrik der Zukunft bietet.
Zielstellung
Ziel ist es, eine interdisziplinäre Forschungsumgebung zu schaffen, mit Fokus auf den Themenbereichen der Industrie 4.0: Smart Factory, Smart Operations, Smart Products, Data-driven Services, Smart Worker und Digital Leadership. Hierfür werden im Projekt neue Transfer- und Informationskonzepte entwickelt. Ein Beispiel hierfür sind Co-Creation-Workshops, in denen sich Unternehmen über neue und innovative Lösungen informieren können oder auch Impulse für neue Projekte und Innovationen geben. Ebenso steht die praktische Demonstration und Erprobung von Lösungen im Fokus des CCL.
Der Projektverbund des CCL profitiert vom Zusammenschluss der Hochschulen und Praxispartner. Durch diesen können eine Vielzahl von Lösungen demonstriert, ausgetauscht und erprobt werden. Auf diese Weise entstehen notwendige Prozessinnovationen, welche von großer Bedeutung für zukunftsorientierte Unternehmen und den digitalen Wandel in der Fertigung sind. Das Co-Creation Lab kombiniert die Expertise aus den Bereichen Automatisierungstechnik, Maschinenbau, Elektrotechnik, Arbeitswissenschaften und Informatik. Daraus resultieren intelligente Systeme für das Zeitalter der Digitalindustrie. In Zusammenarbeit mit Praxispartnern werden in den nächsten 3 Jahren Konzepte und Demonstratoren für die Digitalisierung der Fertigung und Entwicklung neuer Produkte und Dienstleistungen erarbeitet und erprobt. Durch den Wissens- und Erfahrungsaustausch ergibt sich eine Erweiterung der Kompetenzen, welche zu qualitativ hochwertigen Lösungskonzepten führen wird.
Was ist WaPro
Wandlungsfähige Unternehmen, welche agil gegenüber Störungen in den Wertschöpfungs- netzen und ihren Produktionssystemen reagieren können, sind ein Schlüssel für eine krisenfeste Wirtschaft. Sächsische Unternehmen müssen künftig in die Lage versetzt werden, risikobehaftete Veränderungen rechtzeitig zu erkennen und diese zu bewerten. Ihre Produktionssysteme müssen in der Lage sein, auf diese Veränderungen flexibel und agil zu reagieren.
Zur Erreichung der Wandlungsfähigkeit eines Produktionssystems werden in der Literatur fünf Wandlungsbefähiger (Universalität, Mobilität, Skalierbarkeit, Modularität und Kompatibilität) vorgeschlagen. Es gilt, diese Befähiger hinsichtlich ihrer Operationalisierbarkeit für Produktionssysteme von sächsischen KMUs zu untersuchen und geeignete Methoden für die Implementierung der Wandlungsfähigkeit abzuleiten. Die REACT-Forschungsgruppe "WaPro - Wandlungsfähige Produktionsumgebungen" verfolgt dabei einen ganzheitlichen Forschungsansatz, welcher die Wandlungsfähigkeit zur Erreichung aus den Perspektiven Mensch, Technik und Organisation miteinander verbindet. Hierfür wird die Auswirkung des digitalen Wandels auf sozio-technische Produktionssysteme in produzierenden KMUs erforscht. Dabei qualifiziert die Forschungsgruppe künftigen Fachkräfte für die sächsische Wissenschaft und Wirtschaft zur Erforschung und Gestaltung von wandlungsfähigen Produktionsumgebungen als sozio-technische Systeme, welche zur Vorbereitung einer grünen, digitalen und stabilen Erholung der Wirtschaft beitragen.
Das Ziel
WaPro hat das Ziel, den wissenschaftlichen Nachwuchs zur Entwicklung von Konzepten für die Wiederherstellung und Weiterentwicklung einer stabilen, digitalen und grünen sächsischen Wirtschaft zu qualifizieren. Durch die Forschungsgruppe werden neue Konzepte für die Realisierung wandlungsfähiger Produktionssysteme für die diskrete Fertigung in einem interdisziplinären Ansatz erforscht. Mit den Projektergebnissen wird die Innovationskraft des Freistaates Sachsen im Bereich wandlungsfähiger KMUs gestärkt. Hierfür vernetzt die forschungsgruppe die Disziplinen Informatik, Wirtschaftsinformatik, Wirtschaftsingenieurwesen, Betriebswirtschaftslehre, Medieninformatik und Arbeitswissenschaften miteinander.
Abgeleitet aus den Kernzielen ”stabil, grün und digital” werden durch die Nachwuchswissenschaftler die Wandlungsbefähiger Universalität, Mobilität, Skalierbarkeit, Modularität und Kompatibilität hinsichtlich ihrer Eignung zur operativen Umsetzung der Ziele auf den vier Ebenen zwischenbetrieblicher Zusammenarbeit (Vernetzte Wertschöpfung), Fabrikplanung, Maschine/Anlage und Mensch-Technik-Schnittstelle untersucht. Ein wesentlicher Fokus liegt dabei auf der Operationalisierbarkeit der Befähiger für produzierende, sächsische KMU.
Auf der inhaltlich, methodischen Seite ist es das Ziel, Synergien durch die fächerübergreifende Zusammenarbeit zwischen den einzelnen Teildisziplinen zu generieren und die Nachwuchswissenschaftler für die fächer- und methodenübergreifende Zusammenarbeit sowie für die Schaffung von innovativen Lösungen für wandlungsfähige Produktionssysteme zu sensibilisieren und zu motivieren.
Werkzeuge für das Engineering von Digitalisierungslösungen
Das Projekt Arrowhead Tools zielt auf Digitalisierungs- und Automatisierungslösungen für die europäische Industrie. Die technologischen Lücken, die eine IT/OT-Integration behindern, sollen durch Einführung neuer Technologien in einer Open Source Plattform für Design und Laufzeit Engineering von IoT Systemen geschlossen werden. Das Teilvorhaben der HTW Dresden umfasst die Realisierung von Use Cases für die Interoperabilität zwischen sicheren SMART Industrieanwendungen. Aufgabenbereiche umfassen inhaltlich die Unterstützung der Produktion, die Energieeffizienz, das Aufgabenmanagement, die Datenanalytik und smarte Wartung/Instandhaltung.
Mit dem Projekt „Capabilities-bAsed and Self-Organizing Manufacturing Management" (CASO) soll ein Softwareframework entstehen, dass die Fertigungsplanung und -steuerung einer solchen Smart Factory mittels einer kombinierten zentralen und dezentralen Planung unterstützt und die sichere Anbindung von Fertigungskapazitäten von Auftragsfertigern ermöglicht. Das Projekt untersucht die Kombination von Selbstorganisation und zentraler Produktionsplanung in einer Smart Factory, die Möglichkeit zur Beschreibung von Maschinen mittels semantischer Modelle, die darauf basierende dynamisch Generierung von Anlagenrezepten sowie die digitale Absicherung von Rezeptdaten zum Schutz vor Produktfälschungen und dem Schutz von geistigem Eigentum bei Fremdfertigung. Das Projekt wird in Zusammenarbeit mit den Praxispartnern: adidas AG, TecWare Gesellschaft für Softwareentwicklung mbH, DUALIS GmbH IT Solution, Tobias Prometall GmbH & Co. KG und Carl Zeiss Innovationszentrum für Messtechnik GmbH durchgeführt.
SmaRTHI steht für Smarte Robotik für zeitflexible, immersive und ortsunabhängige Teamarbeit in Handwerk und Industrie und ist ein gemeinsames Projekt der TU Chemnitz, TU Dresden, HTW Dresden und des Fraunhofer IWU gewesen im Rahmen der Zukunftscluster-Initiative (Clusters4Future) des Bundesforschungsministeriums. Das Ziel: Menschen und Roboter arbeiten enger zusammen, um die Wettbewerbsfähigkeit von Handwerk und Industrie zu steigern. Die Vision des Zukunftsclusters SmaRTHI ist es, dass Menschen und Roboter zukünftig als sich optimal ergänzende zeitflexible und ortsunabhängig Teams zusammenarbeiten. So können bessere Arbeitsbedingungen geschaffen werden, der Mensch bei seinen manuellen Tätigkeiten geschützt, die Teilhabe am Arbeitsmarkt demokratisiert werden und auch dem Fachkräftemangel im Handwerk soll mit den neuen Technologien etwas entgegensetzt werden. Gleichzeitig werden die Fabriken und Betriebe effizienter, flexibler und resilienter. Im Ergebnis kann der gesamtgesellschaftliche Wohlstand gesteigert werden. SmaRTHI baut ein Ökosystem auf, in dem neuartige Technologien erforscht, entwickelt und industrialisiert werden. Der Digitalisierung als verbindendes Element wird verstärkt zu einer wertschöpfenden Wirkung in physischen Prozessen verholfen.
Aktuelle Informationen zum Forschungsverbund finden Sie hier im Web: https://www.smarthi.de/
Intelligente Automatisierung des Reifenmontageprozesses
Motivation und Zielstellung
Ziel des Projektes ist es, durch smarte Automatisierung des Reifenmontageprozesses eine kontinuierlich hohe Qualität zu sichern, die Quantität zu steigern und somit die Kundenzufriedenheit zu erhöhen. Hierfür entwickelt das Projekt Funktionsmuster und Demonstratoren, welche eine Automatisierung des Montageprozesses unter Nutzung bereits heute in der Montage genutzter Anlagen ermöglichen. Diese Anlagen werden im Sinne eines Retrofit-Ansatzes um Sensoren und Aktoren erweitert. Mit einer solchen Anlage werden die körperlich schweren Arbeiten von den Mitarbeitern auf den Montageautomaten verlagert und sehr hohe, gleichbleibende Qualität sowie höherer Durchsatz möglich.
Teilprojekt: Softwaresysteme und Testumgebung für die RFID-Sensortag-Plattform
In RISE4PM werden neue Methoden für die Nutzung von drahtlosen RFID-Sensorsystemen zur Realisierung von Industrie 4.0-Anwendungsfällen untersucht. Hierfür sollen neue Ansätze in Form von Cyber-Physischen-Systemen für die Produktion erforscht und entwickelt werden. Im Ergebnis entsteht ein holistisches Framework eines Cyber-Physischen-Production-Systems (CPPS) aus Hard- und Softwarekomponenten, welches industrielle Anwender in die Lage versetzt, typische Messaufgaben für Industrie 4.0-Anwendungsfälle einem Plug-and-Work-Ansatz folgend unter Nutzung von RFID-Technologien, effizient zu realisieren.
Transferzentrum Funktionsintegration für die Mikro/Nanoelektronik - Teilprojekt SimiKom - Systemintegration miniaturisierter Komponenten für strukturintegrierte, drahtlose Sensorik im Maschinenbau
In Zusammenarbeit mit dem Fraunhofer IPMS entwickelt die HTW Dresden unter Nutzung der in SimiKom entwickelten Technologien einen drahtlosen Datenlogger mit einer RFID-Sensorik-Schnittstelle, welcher sich nahtlos in den Materialfluss in einem Fertigungssystem (z.B. durch Anbringen am Bauteil oder als separaten „Auftrags“ im System). Das Projekt entwickelt und erprobt hierfür neue Softwarearchitekturen zur effizienten Erfassung und Verarbeitung von Sensordaten. Ein weiterer Arbeitsschwerpunkt liegt auf der Entwicklung einer Verwaltungsschale für den Datenlogger und das Gesamtsystem für eine nahtlose Integration in betriebliche Informationssysteme und industrielle Steuerungen.
Moderne Lehre braucht einen zeit- und ortsunabhängigen Zugang zu Lernressourcen und -inhalten. Aktuell sind diese Lernumgebungen primär auf digitale Inhalte und Formate beschränkt. Mit dem Projekt „Ubiquitous learning environment for cyber physical systems" (ULE4CPS) wurden neue Formen der Interaktion beim Lehren und Lernen an Cyber-Physischen-Systemen (CPS) ermöglicht. CPS sind Systeme, bei denen informations- und softwaretechnische mit elektronischen und mechanischen Komponenten verbunden sind. Während in der Praxis die Arbeit mit digitalen Zwillingen und virtueller Inbetriebnahme zunehmend an Bedeutung gewinnt, existieren kaum Arbeiten, welche diese Konzepte für die Anwendung in die Hochschulbildung übertragen. Das Projekt soll, zusätzlich zur Präsenzlehre für Lernende, zu jeder Zeit und an jedem Ort den Zugang zu komplexen technischen Systemen ermöglichen. Ziel war die Schaffung einer Lern- und Experimentierumgebung, mit der zeit- und ortsunabhängig die mentale und physische Immersion in komplexe informationstechnische und physische Systeme ermöglicht wurden.
Das Projekt ULE4CPS wurde im Rahmen der Jubiläumsinitiative "Wirkung hoch 100" des Stifterverbandes, als eine der 100 herausragendsten Ideen für bessere Bildung, Wissenschaft und Innovation gefördert.
Zur individuellen Ermittlung des digitalen Status eines Unternehmens
(digitaler Reifegrad) wurde im Rahmen des Projektes "DigiLotse" das
gleichnamige Selbstbewertungstool entwickelt. Dieses Tool bietet
neben der Einschätzung des digitalen Reifegrades auch passende,
zielorientierte Handlungsempfehlungen, die durch konzipierte
Demonstratoren und Erklärungen veranschaulicht werden. Dadurch
soll Unternehmen der Einstieg in die Digitalisierung erleichtert werden.
Mehr Informationen zum DigiLotsen und den Zugang zum Tool finden Sie hier.
Motivation
Moderne Produktionsanlagen sind heutzutage ohne Roboter nicht mehr denkbar. Durch eine hohe Zuverlässigkeit, geringe Ausfallzeiten und das Arbeiten in Gefahrenbereichen sind Roboter der Garant dafür schnelle Produktion in hohen Stückzahlen zu ermöglichen. Robotern wird dabei nachgesagt, sie würden Arbeitsplätze vernichten. Die Praxis zeigt jedoch, dass das nicht der Fall ist. Vielmehr schaffen sie Arbeitsplätze. Ohnehin ist aktuell der Trend erkennbar, dass Produktionsprozesse im Zuge der Digitalisierung der Industrie sehr viel individueller werden. Roboter können mit diesen häufigen Änderungen bisher nicht umgehen und müssen deshalb ständig neu programmiert werden. Der dadurch entstehende Implementierungsprozess ist sehr komplex, teuer und langwierig. Aktuelle Marktzahlen belegen, dass ca. 56% der Kosten bei der Automatisierung einer bisher manuell ausgeführten Tätigkeit durch die Umsetzung der notwendigen Software entstehen. Die Kosten für die Automatisierung können so auf ein Maß ansteigen, in dem sich diese nicht mehr lohnt.
Vor allem die Anpassungsfähigkeit von Menschen und deren Fähigkeit zur kreativen Problemlösung sind für heutige Produktionsanlagen unverzichtbar. Roboter sollten vielmehr dafür eingesetzt werden die Arbeit von Menschen zu erleichtern. So können diese den Teil der Arbeit erledigen, der besonders schwer, gefährlich oder monoton ist. Dazu müssen Roboter in die Lage versetzt werden schnell und adaptiv mit Menschen zu kollaborieren. Sogenannte Cobots sind genau dazu im Stande. Der Vorteil einer Kollaboration ist, dass Übergaben zwischen manuellen und automatisierten Produktionsschritten direkt ausgeführt werden können und unter Umständen auch kollaborative Manipulationen möglich sind. Der Bereich der Mensch/Roboter Kollaboration wird aktuell noch weitestgehend unbeachtet. Die Umsetzung und Etablierung dieser Schlüsseltechnologie würde die hiesigen Unternehmen auf dem internationalen Markt wettbewerbsfähig halten und auf diese Weise nachhaltig Arbeitsplätze sichern.
Zielstellung
Im Rahmen des Projektes soll ein Demonstrator entwickelt und in die Industrie 4.0 Modellfabrik integriert werden, welcher die Zusammenarbeit zwischen einem Cobot und einem Menschen an einem Handarbeitsplatz ermöglicht. Um dem hohen Kosten- und Zeitfaktor bei der Roboterprogrammierung entgegenzuwirken, wird die Lösung des Konsortialführers Wandelbots GmbH genutzt, mit der Nicht-Programmierer mit Hilfe intelligenter Kleidung und Gestenerkennung in die Lage versetzt werden Industrieroboter anzulernen, ohne dabei Programmcode schreiben zu müssen. Dabei soll die technische Integration der Sensorkleidung, der Cobot-Steuerung und der RTLS mit einem Fertigungssteuerungssystem entwickelt und erprobt werden. Im Ergebnis entsteht ein Demonstrator, welcher im Zusammenspiel aus Sensorinformationen aus der Kleidung, den Informationen aus den RTLS und den jeweiligen Auftragsinformationen aus dem Fertigungssteuerungssystem eine optimale und auf den jeweiligen Werker individuell angepasste Unterstützung durch den Cobot an einem Handarbeitsplatz ermöglicht. Durch die Integration in den Smart Systems Hub Dresden kann der Demonstrator in vielerlei Hinsicht weiterverwendet werden. Vorranging kann er als Blaupause für andere lokale Unternehmen dienen und demonstrieren wie kollaborative Robotikanwendungen in Produktionsanlagen gestaltet, geplant und kostengünstig umgesetzt werden können.
Durch die rasante Verbreitung im Alltag und die große Akzeptanz bei den Nutzern werden digitale Assistenten zu einem allgegenwärtigen Teil unseres Lebens. Der Erfolg der intelligenten Assistenten ist auf das intuitive Benutzerinterface zurückzuführen. Die Sprache ist als natürlichste Kommunikationsform zwischen Mensch und Maschine zu betrachten. Das Sprachinterface erlaubt eine beiläufige und einfache Nutzung von Geräten auch für unerfahrene und wenig technikaffine Nutzer. Aufgrund der Komplexität der natürlichen Sprache wurden sprachbasierte Assistenzsysteme zur Steuerung und Kommunikation in der Fertigung bisher nicht eingesetzt. Zielsetzung des Debuti Projektes ist die Recherche zum aktuellen Stand von sprachgesteuerten Assistenzsystemen in der Fertigung, die Konzipierung und Umsetzung eines Demonstrators zur Kontrolle eines Roboters durch einen sprachgesteuerten Assistenten sowie die Vorbereitung eines Forschungsvorhabens für den Einsatz von digitalen, sprachgesteuerten Assistenzsystemen in der Fertigung.
Camouflage - Arbeitsplatz 4.0 Berührungslose Nachverfolgung am Arbeitsplatz
Motivation
Ein durchgängig etabliertes Qualitätsmanagement ist die Grundvoraussetzung zur Sicherung einer nachhaltigen Wettbewerbsfähigkeit in einem produzierenden Industriebetrieb. Der damit verbundene organisatorische und technische Aufwand zur Erhebung und Verarbeitung dieser Daten stellt in erster Linie kleine und mittlere Unternehmen (KMU) vor erhebliche Herausforderungen. Während High-Tech-Unternehmen wie bspw. der Halbleiter- und Automobilindustrie auf eine direkte und automatisierte Datenerfassung von der Maschine an das Fertigungsleitsystem (engl. Manufacturing Execution System - MES) setzen, werden die Daten bei KMU meist manuell durch den Werker mittels eines Bedienterminals bzw. papiergestützt gepflegt und nachhinein digitalisiert. Die Nachteile dieser Erfassungsmethode reichen vom teilweisen und gänzlichen Fehlen von Daten, zeitlichen Abweichen von realen Bearbeitungszeiten bis hin zur Steigerung des Risikos von Erfassungsfehlern durch den Werker. Insbesondere eine auftrags- und vorgangsbezogene Rückmeldung ist häufig nicht möglich, da hierdurch der eigentliche Fertigungsprozess unterbrochen wird, folglich eine durchgängige und effiziente Fertigung unmöglich ist.
Zielstellung
Dieser Problemstellung begegnet der im Forschungsprojekt zwischen der HTW Dresden und dem Unternehmen camLine Dresden GmbH konzipierte Prototyp zur innovativen Arbeitsgestaltung im Sinne von Industrie 4.0. Mithilfe einer Software zur Echtzeit-Analyse von dreidimensionalen Tiefendaten und der Anbindung an ein MES können der Materialfluss am Arbeitsplatz durchgängig erfasst und Arbeitsvorgänge berührungslos überwacht werden.
- Automatisierten Überwachung der Materialentnahme und -verbuchung im IT-System des Unternehmens
- Teilautomatisierte Zuordnung der Materialqualität durch Ablegen des Werkstücks in definierten Arealen des Montagebereiches
- System unterstützt den Werker konkret beim Rüsten und Umrüsten des Arbeitsplatzes, dokumentiert den Beginn, das Ende und ggf. den Abbruch eines Arbeitsvorgangs und kann dem Werker auf Wunsch eine Montage-Anleitung oder serielle, interaktive Echtzeit-Hilfe zum Montage-Prozess anbieten
- Anwendung ohne ständige Medienbedienung und Prozessbrüche
- kontaktlose und störungsfreie Erfassung aller notwendigen Informationen für eine lückenlose Nachverfolgung, eine direkte Überprüfung des aktuellen Prozesszustandes sowie die zeitnahe Rückmeldung von Fertigungsaufträgen am Arbeitsplatz
- durchgängigen Arbeitsfluss sowie Produzenten und Kunden Transparenz bezüglich der Fertigungsvorgänge.
Motivation
Ein Drittel des globalen Energieumsatzes wird für die Herstellung von Gütern verwendet. Gerade deshalb steht die "industrielle Fertigung" im Fokus der Bemühungen um mehr Energieeffizienz. Die begrenzt verfügbaren Ressourcen sowie die Probleme der globalen Erwärmung stellen dabei nicht zu unterschätzende Herausforderungen dar. Die steigenden Energiepreise üben zudem Druck auf den industriellen Sektor aus. Diese stellen heute in den meisten Unternehmen den zweitgrößten Kostenfaktor, noch vor den Personalkosten, dar. Führungskräfte weltweit haben dies erkannt und sind mehrheitlich der Meinung, dass die Effizienz hinsichtlich aller Energieträger in den nächsten 20 Jahren einen kritischen Faktor für ihr Unternehmen darstellen wird. Deutschland versucht auch hier eine Führungsrolle einzunehmen, indem Maßnahmen zur Verringerung des Energiebedarfs gefördert werden. In den Umsetzungsempfehlungen für das Zukunftsprojekt Industrie 4.0 ist genau diese Strategie definiert. Noch steht Deutschland dabei am Anfang seiner Bemühungen. Bisher konsumiert die deutsche Industrie noch ungefähr 46% der Gesamtenergie. Davon werden nur zwischen 10% und 15% für die eigentlichen Arbeitsschritte an den produzierenden Maschinen genutzt. Es besteht somit ein großes Potenzial zum Handeln.
Zielstellung
Ziel des Verbundprojektes zwischen der HTW Dresden und der ccc software gmbh ist es, die aus unterschiedlichen Quellen u. a. Sensoren stammenden Messwerte, Prozess- und Energieverbrauchsdaten mit modernen Methoden zu analysieren, aufzubereiten und daraus Handlungsvorschläge für Prozessingenieure, Anlagenverantwortliche sowie Manager von KmUs abzuleiten. Somit werden die Entscheidungsträger in die Lage versetzt, selbstständig zu handeln und „Energiesünder“ zu erkennen, Fertigungsabläufe zu optimieren oder bspw. den Hauptverbrauch in Zeiten mit günstigem Energietarif zu verlegen. Auf Grundlage historischer Daten sollen Modelle entwickelt werden, welche dem Kunden bei der Planung einer energieeffizienten Fertigung unterstützen. Hierfür müssen die Daten für die Weiterverarbeitung aufbereitet werden, indem sie gefiltert und um weitere Daten angereichert oder in eine auswertbare Form umgewandelt werden. Auf Grundlage dieser Informationen und durch unterschiedliche Verfahren kann die Ausbeute der Produktion bei gleichem oder geringerem Energieaufwand verbessert werden. Eine moderne Fertigung bietet viele Ansatzpunkte: So könnte sich zum Beispiel die Verringerung von Ausschuss und Nacharbeit positiv auf den Gesamtverbrauch des Unternehmens auswirken. Des Weiteren lassen sich durch die Optimierung von Prozessparametern und den damit einhergehenden Energieeinsatz Einsparpotentiale erzielen. Die Ansätze sind dabei vom konkreten Anwendungsfall unabhängig und lassen sich somit auf verschiedene produzierende Unternehmen anwenden. Das Bestreben des Forschungsprojektes ist es, KmUs, welche die Software der ccc gmbh nutzen, dank eines geringen Zeit- und Ressourcenaufwand, der normalerweise mit Optimierung einhergeht, eine Senkung ihres Energieverbrauches zu ermöglichen und somit auch zum gesamtdeutschen Ziel der Energieeinsparung beizutragen.
Motivation
Im Zuge der Automatisierung von Produktionsanlagen wird Sensortechnik zur Überwachung und Sicherung der Produktionsprozesse immer wichtiger. Bisher am Markt verfügbare Lösungen konzentrieren sich auf die Möglichkeit der externen Produktfertigungsüberwachung. Intelligente Sensoren hingegen ermöglichen es, dass sich herzustellende Produkte selbstständig lokalisieren sowie Informationen aus der Umgebung erfassen können und damit in der Lage sind, ihren eigenen optimierten Weg entlang des Fertigungsprozesses zu bestimmen. Um die Abmaße der Sensoren dabei möglichst gering zu halten ist es notwendig, den Energieverbrauch zu verbessern, um die mitzuführende Energiequelle klein zu halten.
Zielstellung
Das Projekt legt den Fokus auf die Entwicklung einer Sensorplattform, welche drahtlos lokalisiert werden kann und energieeffizient Sensorwerte aus ihrer Umgebung aufnimmt und überträgt. Das Projekt entwickelt hierfür Methoden, um den Energieverbrauch auf der mobilen Plattform signifikant zu senken. Hierfür werden die Kompetenzen in der Sensorplattformentwicklung mit der Expertise bei der Lokalisierung und der Expertise in der Datenanalyse, -vorverarbeitung und -aggregation miteinander kombiniert.
Verteilte Produktionsplanung mittels paralleler multikriterieller evolutionärer Algorithmen
Motivation
Eine leistungsfähige Industrie ist und bleibt für eine moderne Volkswirtschaft wie Deutschland unverzichtbar. Sie muss sich heute stets neuen Anforderungen stellen, um ihre Spitzenposition auf dem Weltmarkt zu behaupten. Die Unternehmen stehen dabei u.a. vor den Herausforderungen bei gleichen Kosten ihre Produkte kundenindividueller, ressourcenschonender und zuverlässiger zu produzieren. Um diesen Herausforderungen zu begegnen, müssen sie neuartige Lösungen einführen, die in der Lage sind die Produktionsabläufe effizient zu steuern. Das Promotionsverfahren adressiert den Teilbereich der Produktionsplanung und hat zum Ziel, neue Verfahren für die effiziente Planung der Produktionsabfolge für diskrete Fertigungsprozesse zu entwickeln. Gleichermaßen sollen die zu entwickelnden Verfahren produzierende Unternehmen in die Lage versetzen, mittels schneller und effizienter Planungsverfahren eine optimale Bearbeitungsreihenfolge in der Fertigung zu bestimmen. Dabei sind häufig mehrere Zielkriterien, wie z.B. kurze Durchlaufzeiten, hohe Kapazitätsauslastung, eine hohe Termintreue oder geringer Energieumsatz, die es zu optimieren gilt, gleichzeitig von Belang. Besonders, wenn neben den wirtschaftlichen Kriterien gleichzeitig der Energieverbrauch betrachtet werden kann, ist es möglich einen Beitrag zu einer ökologisch nachhaltigen Produktion zu leisten. Hinzu kommen Restriktionen, wie z.B. die Verfügbarkeit von Ressourcen, die den Lösungsraum einschränken. Dieses Problem wird durch eine heuristische multikriterielle Optimierung angegangen.
Zielstellung
Um einen ausführbaren Fertigungsplan zur Verfügung zu stellen, werden multikriterielle parallele Problemlösungsansätze, die verschiedene Zielgrößen der Produktionsplanung parallel betrachten, genutzt und damit eine höhere Lösungsqualität zu erzielen. Zusätzlich kann so erreicht werden, dass die Zeit, bis eine akzeptable Lösung vorliegt, verkürzt wird. Dazu wird an Vorarbeiten aus der Wissenschaft im Rahmen des Projektes angeknüpft, mit dem Ziel diese weiterzuführen und an das vorliegende Problem anzupassen. Die wissenschaftlichen Arbeitsmethoden beinhalten insbesondere eine begleitende Validierung, Verifizierung und Qualitätskontrolle für jeden Arbeitsschritt und einen starken Fokus auf fortlaufende Dokumentation und Veröffentlichungen. Zudem findet begleitend eine stetige Auseinandersetzung mit aktuellen Entwicklungen auf dem Gebiet statt, so werden weiterverwendbare, nachvollziehbare und hoch qualitative Ergebnisse gesichert. Als Resultat wird eine Metaheuristik in Form eines parallelen multikriteriellen evolutionären Algorithmus erwartet, die effizient arbeitet und in der Lage ist, bessere Ergebnisse in kürzerer Zeit als etablierte Methoden zu liefern. Sie soll an verschiedene Problemstellungen anpassbar, einfach nutzbar, getestet, dokumentiert und veröffentlicht sein. Es ist geplant, die zu entwickelnde Software unter eine Open-Source Lizenz zu stellen, und damit sächsischen Unternehmungen einen einfachen Zugang zu den Arbeitsergebnissen zu ermöglichen. Weiterhin wird eine Trennung zwischen der Simulation und dem Optimierungsverfahren angestrebt, so dass ersteres ausgetauscht werden kann. Die Kommunikation zwischen den Instanzen soll effektiv ablaufen, so dass eine hohe Performance erreicht wird, die im Vergleich bessere Ergebnisse bei begrenzter Zeit liefert. Der Algorithmus soll zudem unabhängig von bestimmten Soft- und Hardwareplattformen anwendbar sein. Die Ergebnisse werden in Form von Journalbeiträgen und nationalen und internationalen Konferenzbeiträgen (Evostar, GECCO, AKWI) veröffentlicht. Darüber hinaus sollen die Arbeitsergebnisse frühzeitig den sächsischen Unternehmen zugänglich gemacht werden. Dies soll u.a. in Form von Open Access und Fachvorträgen bei Veranstaltungen des Silicon Saxony erfolgen. Die Fortsetzung des Projektes ist nach Abschluss der Promotion an der Professur von Prof. Reichelt an der HTW Dresden geplant. Das betrifft die Pflege und Weiterentwicklung der Ergebnisse und weitere Forschungsprojekte, die im Anschluss darauf aufbauen.